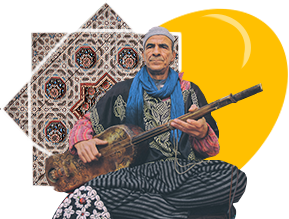
Marrakech Desert Tours: Morocco Adventure Tours
Welcome to the Desert Morocco Adventure Tours site! The best place for private Marrakech desert tours and excursions through Morocco. You’ve never been on a real adventure until you’ve visited the fairytale medieval medinas, the majestic Sahara desert, and the seductive shores of the dazzling North African country of Moroccan. Filled with exotic tastes, exquisite crafts in the ancient maze-like souks, and stunning scenery, Morocco is the dream destination for adventurers.
Morocco is an interesting blend of the African, Berber, and Arab worlds, featuring modern cities like Casablanca, juxtaposed against small nomadic villages in the mountainsides and the Sahara Desert. Spend lavish days in the vibrant red city of Marrakech enjoying fine dining, ample shopping opportunities, vibrant nightlife, and spa experiences interspersed with fascinating cultural sites.
Escape the hustle and bustle of the city and head out to experience the majestic Sahara Desert. Ride camelback through the shifting sands of the tallest dunes of Morocco, marveling at its untouched beauty. If time allows, visit the serene coastal villages or find peace in the beautiful blue city of Chefchaouen- a photographer’s dream.
Mixing ancient culture and modern conveniences, Morocco’s popularity is on the rise. It is one of the top 20 travel destinations. What are you waiting for, pack your bags, and let us at Desert Morocco Adventures plan an epic Moroccan adventure for you!
Desert Morocco Adventure is proudly managed by DM-Adventure SARL, a trusted privately owned company duly incorporated and registered in Morocco under the official registration number 2907. Choose us for unforgettable desert experiences with confidence. Book now for an extraordinary journey!
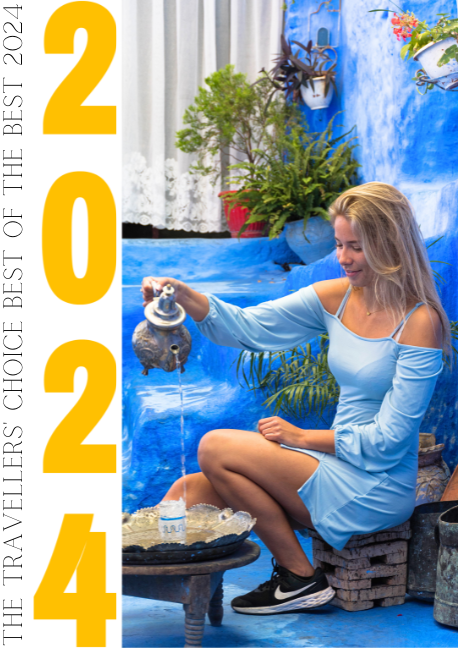
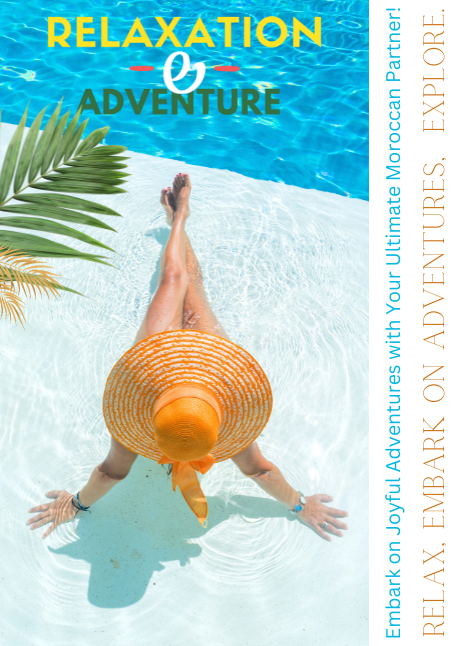
About Desert Morocco Adventure Tours
Your ultimate partner for fun, exciting, and affordable adventurous Sahara Desert excursions in Morocco, where relaxation meets exploration. Let us show you the magic of the real Morocco through the eyes of the locals and make your Moroccan travel dreams come true, all while offering serene and relaxing experiences amidst the wonder of Morocco.
Inspired by our love for all matters related to adventure travel and Morocco, our team and friends happily share their best-kept travel secrets here on the Desert Morocco Adventure site. We strive to be an honest, authentic, and hospitable company. Our responsibility is to ensure that the adventurers who travel with us, travel with a sense of comfort and peace of mind. Comfort, safety, and well-being are our top priorities. – willing to go above and beyond to satisfy our customers.
We are a well-established, internationally recognized, and award-winning Moroccan-based adventure tour company. We’re seasoned world travelers. Our goal is to provide an experience that will meet or exceed the requirements of our guests by providing expertly curated tours.
Our passion is to provide you with all the information regarding the best places to visit and enjoy during your stay in Morocco. Whether you stay at one of our partner accommodations or travel with us on one of our world-famous Moroccan desert adventure tours, we want you to have the most amazing vacation and an unforgettable experience.
We love this charming country with its exciting natural landscapes and we want to share that love with you. Should you need any advice on traveling in our beloved country, please feel free to drop us a line or chat with our friendly travel experts – Ask us anything you would like to know about adventure travel in Morocco.
Cultural Immersions with
Locals
Most Popular Morocco Tours & Marrakech Desert Trips
At Desert Morocco Adventure we organize daily private tours through Morocco and marvelous trips from Marrakech to the Sahara desert. We have various Morocco tours and outdoor activities available that can be booked all year round. Our trips are private, with just you and a friendly and knowledgeable English-speaking driver/guide in an air-conditioned vehicle.
Do you need a well-organized customized travel plan? Our experienced Morocco travel planners are happy to help you organize exciting Morocco tour itineraries. Travel around your favorite destination for day trips or multi-journey round trips from the most popular Moroccan vacation destinations below:
FAQ - Desert Morocco Adventure Tours
What's the weather like in the Sahara Desert?
The temperature of the Moroccan Sahara Desert is sunny and hot from June to mid-September, both during the day and at night as well, reaching around 45 degrees Celsius during the day and around 30 degrees Celsius at night. The highest temperature the Sahara has ever seen is 58 degrees Celsius. It gets cool temperatures from November to March at night and warmer during the day, hovering around 27°C and dropping dramatically to about 0°C at night. In the other months, the daytime temperature is usually about the same as that of the night, varying around 25 to 30 degrees Celsius.
Can I join a Marrakech Sahara desert trip?
We are sorry, we currently only organize private tours and trips around Morocco, and our tours can be booked at any time. We also offer 4x4s with a professional English-speaking driver/guide for hire for private individuals and also for travel agencies. You travel alone with your driver/guide in a very comfortable and safe four-wheel drive. Usually, it is Icho who guides and takes care of our customers.
Can you arrange a tailor-made Moroccan trip?
Yes, we are happy to arrange a tailor-made Moroccan trip to suit your needs and wishes. If you have not found a Moroccan tour that includes all the interesting sites you would like to see, we can create together an itinerary via chat or email and suggest you different tours and ideas until you find the right one for you. All of our tours available on the website can be combined or even added more days or locations at the request of our customers. The customer is King!
How do I book Marrakech Desert Tours?
To reserve your spot on any Marrakech Desert Tour, simply head to the tour details page or reach out to us via email. To confirm your booking, we kindly request a deposit of at least 21% of the total tour cost.
What language do they speak in Morocco?
Morocco officially has two languages (classical Arabic and Tamazight), but in daily life, it is another story, it’s a mixture of languages. Most Moroccans speak Darija and Berber in addition to other foreign languages. French seems to be the second language as it is a business language in the country. Most Moroccans also speak French and Spanish in the north of the country and in the Sahara. English is very popular among the young generation and workers in the tourism industry. Visit this page to learn more about the languages commonly spoken in Morocco
What They Say About Our Marrakech Desert Trips
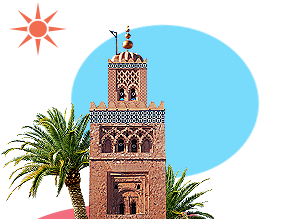
Recent posts on the Desert Morocco Adventure Tours blog
Read about the latest travel inspiration on the Desert Morocco Adventure blog. Through our blog, we share helpful tips and honest reviews, focusing on topics such as Morocco Tours, Tourism Transport, Travel Tips, Moroccan Food, and various locations. Check out our Morocco Travel blog posts to read more about this mystical country. If you would like to share your travel experience in Morocco with us, please feel free to contact us.
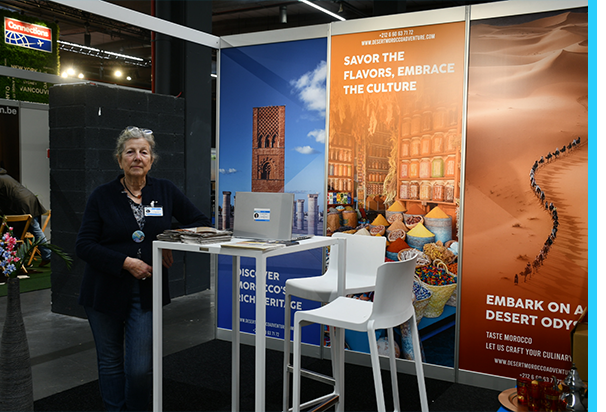
Let Us Plan Your Perfect Marrakech Desert Trip!
Are you in search of a meticulously planned desert adventure in Morocco? Our exceptional team is eager to assist you in orchestrating every aspect, from accommodation to transportation. Whether you crave exhilarating hikes or serene relaxation, we’ve got you covered!
Explore the sand dunes of the Sahara during a hiking adventure or relax in the peaceful tranquility of the desert. We take care of everything from booking accommodations to arranging transportation so you can fully immerse yourself in the enchanting desert experience. Allow us to customize your desert journey today!
Merhaba! Let the sands be your companion as you embark on an adventurous journey.
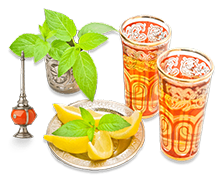